Why Choose Rigid-Flex PCBs?
In today's fast-evolving electronics industry, Rigid-Flex PCBs (Printed Circuit Boards) have emerged as a game-changing solution for high-performance and compact designs. Combining the best of rigid and flexible PCBs, they offer unparalleled reliability, space efficiency, and durability—making them ideal for cutting-edge applications.
This month, we dive into why Rigid-Flex PCBs are the future and how they outperform traditional PCB designs.
What is a Rigid-Flex PCB?
A Rigid-Flex PCB is a hybrid circuit board that combines the benefits of both rigid and flexible PCBs into a single, integrated design. It consists of rigid PCB sections (for component mounting) connected by flexible circuit layers, allowing the board to bend or fold while maintaining electrical connections.
Key Advantages of Rigid-Flex PCBs
1.Space & Weight Reduction
Eliminate bulky connectors—Seamless transitions between rigid and flexible sections and reduce assembly size.
Lighter than rigid PCBs-Perfect for aerospace, wearables, and portable devices.
Example: A medical wearable using Rigid-Flex PCBs reduced weight by 30% compared to traditional designs.
2.Enhance Durability & Reliability
Fewer solder joints -Lower risk of failure due to vibration/shock.
Bendable without cracking -Withstands 100,000+ flex cycles (IEC 60112 tested).
Better thermal performance -Efficient heat dissipation in high-power applications.
Case Study: Automotive control modules using RigidFlex saw a 40% drop in field failures.
3. Simplify Assembly & Lower Costs
Fewer interconnects-Reduce assembly time and labor costs.
Single-unit construction -No need for multiple PCBs + harnesses.
Long-term savings -Higher reliability = lower maintenance costs.
A drone manufacturer cut assembly costs by 25% after switching to Rigid-Flex.
4. Design Freedom for Innovation
3D packaging - Fits into complex shapes (e.g., foldable phones, robotic arms).
High-speed signal integrity - Minimizes EMI in 5G/RF applications.
Foldable smartphones rely on Rigid-Flex PCBs for seamless hinge integration.
What Industries Use Rigid-Flex PCBs?
Medical Devices (Hearing aids, endoscopes)
Consumer Electronics (Smartwatches, foldable phones)
Industrial IOT(Robotics, sensors)
Aerospace & Defense (Avionics, satellites)
Automotive (ADAS, EV battery management)
Design Tips for Rigid-Flex PCBs
Bend Radius |
→ Keep ≥ 10x the flex layer thickness to avoid cracking. |
Stiffener Placement |
→ Reinforce high-stress areas (e.g., connectors). |
Material Selection |
→ Polyimide for flexibility, FR4 for rigidity. |
Controlled Impedance |
→ Critical for high-frequency signals. |
POE Rigid-Flex PCB capabilities
Categor |
Process Capability |
Categor |
Process Capability |
Production Type |
Single/Double-sided boards, Multilayer boards, Zinc-plated boards, Layered boards, Rigid-Flex boards, HDI buried hole boards, Special process boards |
Layers |
1-14 layers FPC, 2-14 layers Rigid-Flex boards and HDI buried hole boards |
Max. Production Size |
Single/Double-sided: 250*2500mm, Multi-layer: 500*750mm, Rigid-Flex: 500*750mm |
Insulation Thickness |
27.5μm / 50μm / 75μm / 100μm / 125μm / 150μm |
Board Thickness |
FPC: 0.06-0.4mm, Rigid-Flex: 0.25-6.0mm |
Non-Metal Hole Tolerance |
±0.05mm |
Surface Treatment |
Immersion Gold, Immersion Silver, Electroplating Gold, Electroplating Tin, OSP |
Reinforcement Material |
FR4/ PI/ PET/ SUS/ PSA |
Min. Half-Hole Size |
0.4mm |
Immersion Gold |
Au 0.025-0.075μm/ Ni 1-4μm |
Min. Line Space/Width |
0.045mm/0.076mm |
Electroplating Gold |
Au 0.025-25.4μm/ Ni 1-25.4μm |
Board Thickness Tolerance |
±0.03mm |
Impedance Value |
50Ω-120Ω |
Copper Thickness |
12μm / 18μm / 35μm / 70μm |
Impedance Tolerance |
±10% |
Hole Tolerance (Plated Through Hole) |
±0.05mm |
Min. Slot Width |
0.80mm |
Min. Drilling Size |
0.1mm |
Standards |
GB/ IPC-650/ IPC-6012/ IPC-6013H/ IPC-6013H |
Note: For high-difficulty FPC flexible circuit boards and HDI Rigid-Flex boards, technical evaluation is required based on the documentation. |
Common Stackup For Rigid-Flex PCB
1-layer-flex-with-optional-fr4-stiffeners-and-psa: |
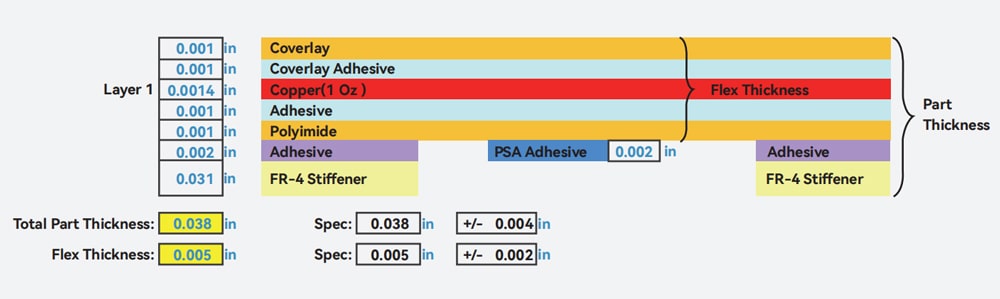 |
2-layer-flex-with-zif-contact-fingers: |
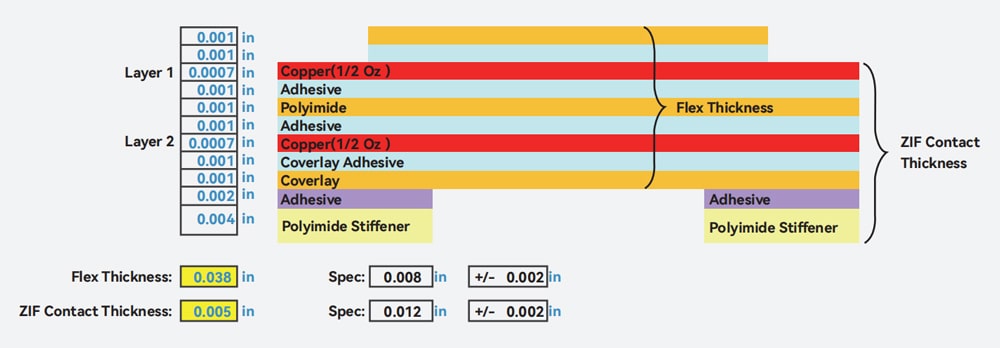 |
4-layer-rigid- flex-stackup: |
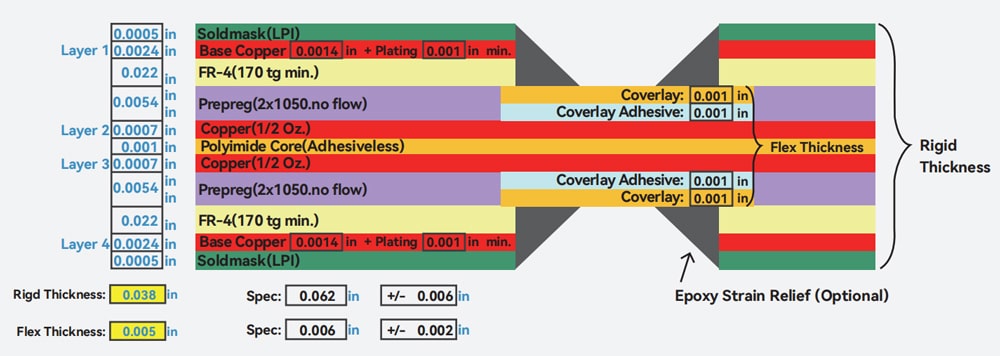 |
Why Us?
We are an ISO 9001:2015 Certified PCB assembly company committed to upholding rigorous quality standards.
With over 20 years of experience in both fabricating and assembling high-quality rigid-flex printed circuit boards, we ensure precision and reliability.
Our state-of-the-art manufacturing facilities are equipped to handle any custom and complex board requirements efficiently.
Our highly qualified team adheres to industry best practices, offering cost-effective solutions tailored to your needs.
Whether you need prototypes or full production runs, you can rely on our comprehensive PCB fabrication services.