Low Volume PCB Assembly: Should You Choose SMT or THT?
21 January 2025
Views: 1702
In low volume PCB manufacturing and assembly, two methods are commonly used: Surface Mount Technology (SMT) and Through-Hole Technology (THT). Both have unique advantages and disadvantages, and your choice between the two can have a significant impact on the final outcome of your project.
What is low volume PCB assembly?
low volume PCB assembly refers to the process of assembling relatively small quantities of PCBs. It is particularly useful for start-ups, small businesses, or projects that require frequent updates and modifications. low volume PCB assembly has many advantages, such as cost reduction, faster turnaround times, greater flexibility, better quality control, improved prototype design, and more.
So, should you use SMT or THT technology in low volume PCB assembly?
What is SMT and THT?
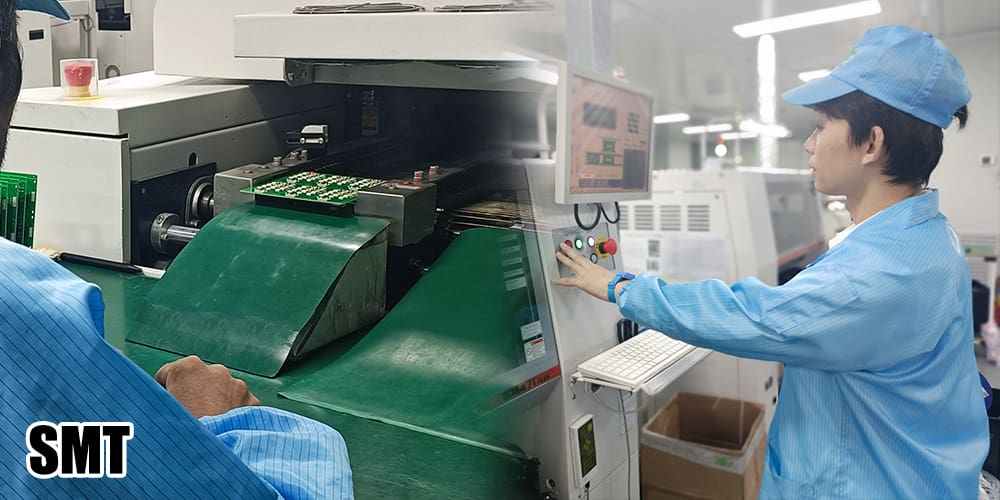
Surface Mount Technology (SMT): SMT is a method of directly mounting components onto the surface of a PCB. SMT allows for high component density and can accommodate both small and large components. SMT has become the industry standard for PCB assembly due to its efficiency and cost-effectiveness in large-scale production.
Advantages and disadvantages of SMT
Advantages:
1.Higher component density: SMT allows for more components to be used per circuit board, which can reduce the size and cost of the PCB.
2.Double-sided assembly: SMT allows for components to be placed on both sides of the PCB, providing additional design flexibility.
3.Improved high-frequency performance: SMT components have smaller leads or no leads at all, reducing inductance and improving high-frequency performance.
4.Economical for large-scale production: SMT assembly is automated, making it more efficient and cost-effective in large-scale production.
Disadvantages:
1.Not suitable for large or heavy components: SMT is not suitable for large components or components that will experience mechanical stress, as the solder connections may not be strong enough.
2.Increased initial setup costs: SMT has higher initial setup costs.
3.Difficult to modify or repair: SMT components are more difficult to replace or repair due to their small size and close proximity to other components.
Through-Hole Technology (THT): THT is a more traditional method of PCB assembly. In this process, components are placed into drilled holes on the board and then soldered onto pads on the other side. THT is typically more time-consuming and expensive, but it offers a strong mechanical bond and excellent electrical connections.
Advantages and disadvantages of THT
Advantages:
1.Strong mechanical bond: THT provides a stronger mechanical bond, making it an ideal choice for components that will experience physical stress or high heat.
2.Easier to modify or repair: Components can be more easily replaced or repaired in THT assemblies.
3.Ideal for prototype design and testing: THT is often used for prototype design and testing due to its flexibility and ease of modification.
Disadvantages:
1.Lower component density: THT has a lower component density compared to SMT, which may result in larger and more expensive circuit boards.
2.Single-sided assembly: Unlike SMT, THT typically only allows for components to be mounted on one side of the PCB.
3.Less cost-effective: THT is more time-consuming and labor-intensive, making it less cost-effective in large-scale production.
How to choose between SMT and THT for low volume PCB assembly?
For low volume PCB assembly, the choice between SMT and THT depends on several factors:
1.If your design requires high component density and frequent operation at high frequencies, or if you plan to scale up production in the future, SMT may be the better choice. However, the high initial setup costs and issues with modifying or repairing circuit boards should also be considered.
2.If your design requires heavy or large components that will experience physical stress or high heat, or if you value ease of modification and repair, THT may be the more suitable choice. Despite its lower component density and higher unit cost, THT's strength and flexibility provide advantages in low volume production, particularly for prototypes or products undergoing testing.
In specific cases, you can also use a hybrid approach (using both SMT and THT simultaneously), which is also a very suitable solution for low volume PCBs. You can take advantage of the strengths of both methods, using THT for components that require a strong mechanical bond or high temperature resistance, and SMT for smaller, more numerous components.
Conclusion
For low volume PCB assembly, choosing SMT, THT, or a combination of both can meet the requirements of most PCB assembly projects. If you have a low volume PCB assembly project or have more questions to ask, please feel free to contact us. POE has more than 20 years of experience in PCB manufacturing and assembly, and we can provide one-stop low volume PCB assembly services. Contact us for more information!
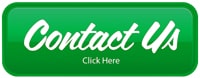